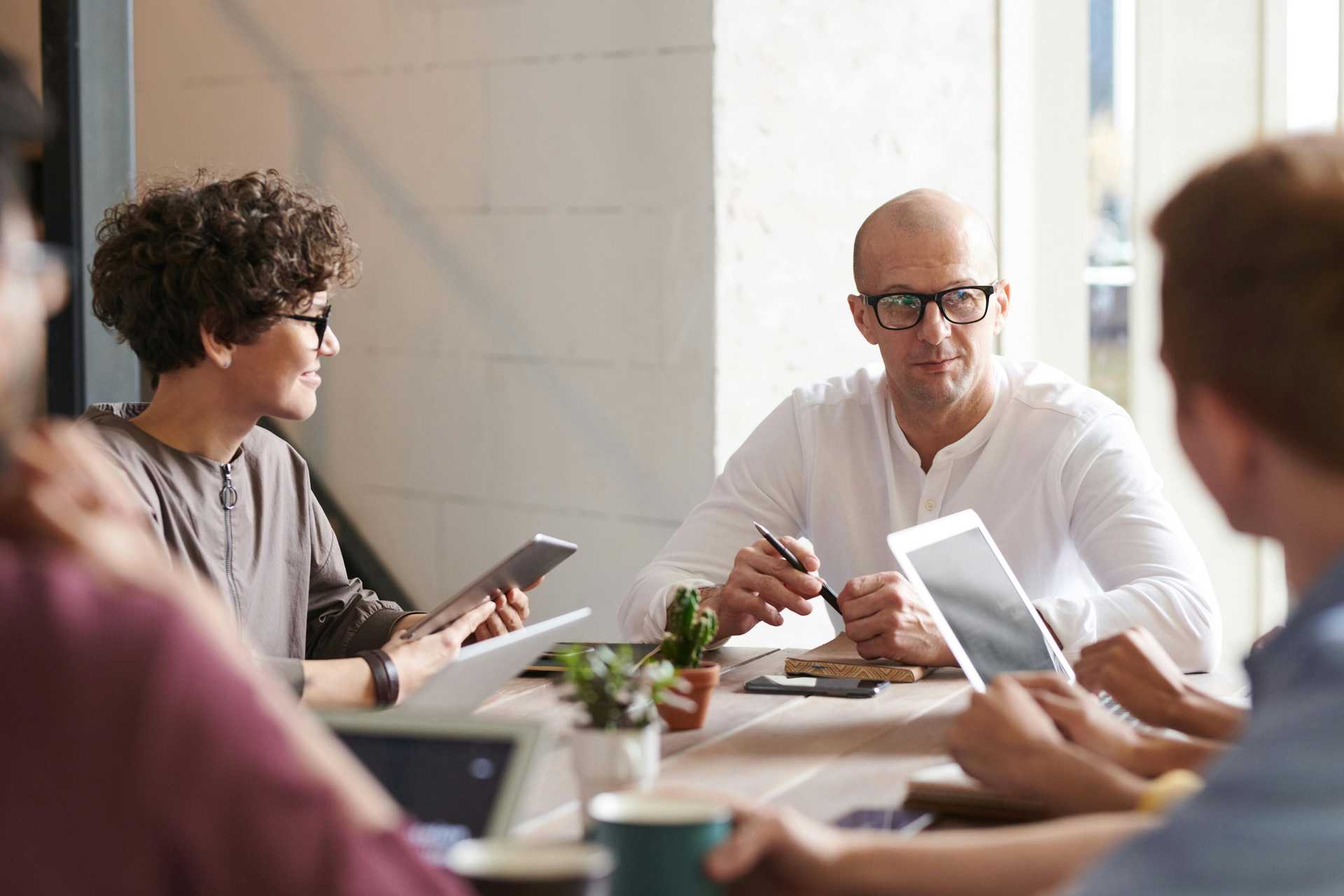
Remote Work and Productivity
Creating a Seamless Onboarding Experience for Remote Employees

Vladana Donevski
Writer and payroll expert
Business Expansion and Growth
Published on:
December 10, 2024
Written by:
Lucas Botzen
Key takeaways
Emerging markets are a cost-effective solution to fill remote manufacturing roles. It is also a good way to manage skill shortages in your local area.
Managing manufacturing remotely can be tricky. It is important to find ways to monitor production and perform predictive maintenance in real-time. Plus, collaborative tools are essential for successful remote operations.
Upskilling workers and creating a hybrid work model will help you stay competitive. Adapting to modern standards and in the evolving manufacturing landscape.
Table of contents
The world is rapidly moving and adapting to remote work. However, remote-first systems can be a struggle to implement well, and employers are consistently trying to find new ways to make it work.
It’s no secret that the manufacturing industry has faced unique challenges in adapting to remote work. However, it’s also an exciting opportunity for businesses like yours to embrace new ways of working. Remote manufacturing roles can solve workforce shortages and reduce costs. It can also open doors to untapped talent in emerging markets.
Shifting to a remote-first model requires overcoming plenty of challenges. These could look like production monitoring, equipment maintenance, or team collaboration. You can adopt the remote model with the right strategy, technology, and mindset. Here's how to transform your business to stay competitive.
Manufacturing is different from industries like IT or marketing, where most tasks can be done online. Your production lines, equipment, and workers are often tied to physical spaces. This makes it extra difficult to adopt remote work practices. Only 41% of manufacturing employees during the pandemic could telework, compared to over 60% in other industries.
This reliance on on-site operations leads to two key challenges:
Limited visibility into production. Without real-time data, managers need to be physically present to monitor production processes.
Talent shortages. Skilled workers are hard to find, and many prefer industries that offer flexible, remote opportunities.
To remain competitive, your business needs to adopt a specific set of tools and practices. It is important to find those who can make remote work possible without sacrificing productivity.
The manufacturing industry is undergoing a remarkable transformation as remote-first models gain traction. Understanding the latest trends can help you stay ahead and adapt your operations to meet modern demands.
One of the biggest hurdles is monitoring your shop floor without being physically present. Fortunately, technologies like IoT sensors and real-time analytics platforms can help. These tools collect data from machines and operators. They also give you a clear picture of your production status no matter where you are.
For example, you can receive automated alerts when a machine breaks down. Or, if production falls behind schedule. This allows you to make quick decisions and minimize downtime, all while working remotely.
Wouldn’t it be great if you could prevent machine failures before they happen? Predictive maintenance tools use data to detect early warning signs of equipment issues. This allows you to schedule repairs in advance. This approach saves money, reduces downtime, and ensures that your operations run smoothly even when you’re not on-site.
Collaboration is key to any successful operation. Tools like video conferencing, messaging apps, and shared dashboards make it easy for your team to stay connected. For example, real-time notifications can alert on-site workers to issues. It will, at the same time, allow remote specialists to provide guidance.
Emerging markets present unique opportunities for manufacturers considering a shift to remote operations. These regions are cost-effective and have talent ready to move to innovative, flexible work models.
Emerging markets are full of skilled workers eager to join global industries. For example, Southeast Asia, Eastern Europe, and Latin America are popular choices. By hiring remotely in these regions, you can access talent that might otherwise be out of reach.
This is especially important given the manufacturing industry’s skills gap. Between 2018 and 2028, an estimated 2.4 million manufacturing jobs could go unfilled. Hiring from emerging markets helps you fill these roles while supporting local economies.
Remote roles in emerging markets are often more cost-effective. You can hire experienced professionals at lower wages compared to developed markets. This allows you to reinvest savings into growth and innovation.
Emerging markets are increasingly investing in training and technology. By tapping into these regions, you can bring fresh perspectives and innovative ideas into your business. This will help you make it more competitive on a global scale.
Making the leap to a remote-first model requires careful planning and strategic decision-making. With the right steps, you can ensure a smooth transition that benefits your business in the long term.
Not every role in your company can be remote, but many can. Start by identifying which positions are most suitable for remote work. For instance, roles in engineering, quality control, and supply chain management often lend themselves to digital workflows.
Next, consider cross-training your on-site workers to handle multiple tasks. This creates a more versatile team that can tackle challenges with fewer people physically present.
A remote-first model requires the right technology. Invest in tools like:
IoT-enabled devices to track machine performance.
Data analytics platforms for real-time insights.
Cloud-based collaboration tools to keep your team connected.
These tools not only make remote work possible but also improve efficiency across your operations.
Upskilling is essential for a successful transition. Train your team to use new technologies and encourage knowledge-sharing across departments. This helps both on-site and remote workers stay productive and aligned.
For example, you can host virtual workshops to teach employees how to interpret production data. It could also be a good solution to troubleshoot equipment issues remotely.
Transitioning to remote work doesn’t stop at adopting new tools. You also need to focus on building a strong, cohesive team culture.
Set clear expectations: Define goals, roles, and responsibilities to avoid confusion.
Communicate regularly: Schedule check-ins and use collaborative platforms to keep everyone informed.
Empower your team: Give on-site workers the autonomy to make decisions. Also, try to ensure that remote specialists have the data they need to support them.
By fostering trust and transparency, you can create a team that works seamlessly across locations.
Remote manufacturing is still in its early stages, but the future is bright. As automation and AI continue to evolve, the industry will rely more on hybrid models that combine on-site and remote work.
Imagine a "lights-out factory" where automation handles repetitive tasks. In such a setting, remote workers can focus on high-value activities like strategic planning. This vision is closer than you think, and by starting now, your business can lead the way.
Shifting your manufacturing business to a remote-first model is a challenge, but it’s also a huge opportunity. By investing in the right technology, training your workforce, and exploring talent in emerging markets, you can build a flexible, competitive, and future-ready operation.
The key is to start small, learn from your experiences, and adapt as you go. Remote manufacturing isn’t just the future—it’s your chance to transform your business today.
How can I identify which manufacturing roles can be remote?
Focus on roles that don’t require physical presence. This could be roles like engineering, quality control, and supply chain management. Assess your team’s tasks and consider using automation for repetitive work.
What tools do I need to enable remote manufacturing?
You’ll need IoT devices, real-time analytics platforms, and collaboration tools. These will help to ensure smooth operations and communication.
Why should I hire from emerging markets?
Emerging markets offer skilled talent at lower costs. It also helps provide access to fresh perspectives and innovative ideas.
Remote Work and Productivity
Vladana Donevski
Writer and payroll expert
International Employment Laws
Vladana Donevski
Writer and payroll expert
Remote Work and Productivity
Lucas Botzen
Founder
We're here to help you on your global hiring journey.